Development of a process model for the logistical implementation of modular production in the process industry
- Simulation and Logistics Engineering
Background
The European process industry is facing increasing global competition. Due to the high availability of raw materials and the steady expansion of production capacities in the emerging markets, European manufacturers are benefiting only insufficiently from the rising demand for petroleum-related basic chemicals. This is leading to an increasing loss of international market shares for the manufacturers of chemical-pharmaceutical products. Due to the background described, European manufacturers are increasingly focusing on the production of higher-value specialty chemicals, where the industrial customer is the driving competitive factor.
Its demand for application-specific and innovative solutions causes the continuous development of product innovations, which results in shorter product life cycles. Therefore, fast and cost-effective adaptations to new production requirements become a crucial competitive advantage.
Modular production plants (see figure) enable the concept of customer-oriented as well as decentralized production and can be adapted to demand fluctuations in a short time. This should secure the competitive advantages of the process industry market for the European manufacturers.
The innovative production form is associated with logistical questions, which must be answered.
Procedure
A detailed analysis of the already existing use cases of modular production forms the basis of the research project. It serves to identify the relevant influencing variables for the design of the logistics structures and processes. Based on this, the essential requirements of the modular production units for their production environment are recorded.
In this way, among other things, the criteria for the selection of a chemical park as well as the positioning of the modular production units within these parks are determined. Furthermore, the design of the supply and disposal processes, as well as the determination of the required operating resources, are also part of the research project.
Targeted results
As part of the research project, it was possible to develop a process model suitable for SMEs (small and medium enterprises) for the logistical implementation of modular production in the chemical and pharmaceutical industry. For this purpose, an Excel-based tool was developed, which contains the results of the work in a compressed form. This tool enables SMEs for the first time to record the necessary logistical requirements for the operation of modular plants. It also provides assistance in the choice of location for small-scale production. Therefore, from a technical and economic point of view, this model simplified the planning of logistical processes that were previously unusual in the industry, which arise with a changeover to adaptable production.
For this purpose, the project analyzed already tested transformable plants and their requirements for logistics and the handling of chemicals. Based on the results of these investigations, the SMEs obtain the necessary overview of the changed logistics requirements. Furthermore, criteria for the selection of suitable production sites for modular production systems were determined, which enabled the SMEs to evaluate the sites. In addition, a simulation study about the conceptual design of production networks shows that a degree of decentralization should be selected, which ensures the shortest possible distance to the customers but also allows a small number of adjustments to the production capacities at the sites. For a more detailed consideration of the logistical framework conditions at the production sites, the necessary logistical and technical infrastructure facilities were identified, which serve the SMEs as a support element in the positioning of the modular plants. Finally, the SMEs get an overview of the various processes for supplying and disposing of the production sites as well as the required operating resources. In view of this, the possibility of outsourcing the logistics services depending on the production location is explained in a structured manner.
The Excel-based tool developed in this research project is available for download. After downloading, please unzip the files contained in the ZIP folder and only then open the tool.
Contact: Prof. Dr.-Ing. Uwe Clausen
Funding and partners
The research project (IGF project no. 19266N) was funded by the German Federal Ministry for Economic Affairs and Climate Action through the Arbeitsgemeinschaft industrieller Forschungsvereinigungen „Otto von Guericke“ e.V. (AiF).
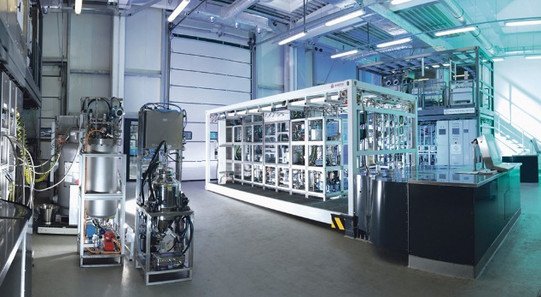